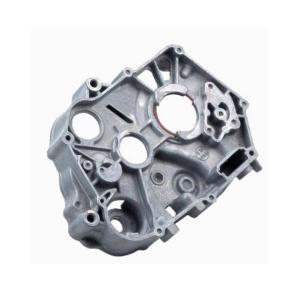
Add to Cart
Lm24 Aluminium Alloy Die Casting Heat Treatment Engine Housing
Aluminium Alloy Die Casting Process
1) Die-casting/ Profile Extrusion
Aluminium Alloy Die Casting Features
1. High Precision, New Technology, Competitive Price for Casting and machining
2. Advanced casting machines available.
3. All kinds of facility, CNC machining, turning, milling, tapping, drilling, polishing, punching, etc...
4. Competitive Prices, Excellent Service.
5. 100% full inspection before shipment.
6. Less than 3% on-time delivery rate.
Aluminium Alloy Die Casting Parameters
Description | Lm24 Aluminium Alloy Die Casting Heat Treatment Engine Housing |
Material | Aluminium: ADC-1,ADC-12,A380, DIN 1706:231,DIN 1706:260,AlSi9Cu3 |
Standard | DIN, AISI, ASTM, BS, JIS, ETC. |
Surface Treatment | Heat Treatment, Polishing, Plating, Machining, Anodizing, Shot, Sand Blasting, Zinc Plated, Oxide, Galvanised Etc. |
Production Application | Metal Parts, Mechanical Parts, Boats , Electric Power Fitting, Construction Parts, Pipe Fitting, Hardware, Auto Parts, Valve Parts, Industrial Parts, Agricultural Machinery, Hinges, Etc |
CNC And MC Machining | Three Coordinate Measurement Machine For Testing. |
Packing Details | Wood Or Carton Packages As Per Your Demands. |
MOQ | Small Order Is Accepted |
Service | Making Machinery Service As Per Your Requirement Or Drawings |
Manufacture Process
1. Review the part design,drawings and quality standard from clients.
2. Mould and Tooling design & manufacturing
3. Mould and Tooling testing & confirm the sample
4. Die casting raw castings
5. Surface treatment: Trimming,Deburring, polishing, cleaning, passivation & power coating and other requirement from Customer
6. Precision machining: CNC lathes, milling, drilling, grinding etc
7. Full Inspection
8. Packing
9. Delivery
Our Advantages
1. We are the biggest lost foam mould manufacturer in China, we focus on high challenge lost foam mould and we have large gantry machining centers,30 sets imported high speed machining center,more than 40 sets general machine tool equipment;
2. We have 36 senior mould designers, to ensure reasonable / safety / high efficiency mould design and ensure the fast mould delivery and rational mould structure, make the process more safer and the production efficiency more higher;
3. We using numerical control machine tool to manufacture the mould cavities, to ensure a even thickness ;
4. We using ZL104 Aluminium to casting the mould, to manufacture a high strength mould;
5. For the big mould, we using Ø22*1 copper tube as cooling pipe, with water spray system, to get a nice cooling effect;
6. We Have (TEF10N) coating on the mould surface, it can reduce the friction, anti water/static electricity/acid-base/high-temperature, with this we can ensure the pattern has smooth surface without distrotion, and easy to demould;
7. All the screws we using stainless steel screw, easy to disassemble during maintenance;
8. For the big mould chest, we using 18-20mm thick wrought aluminium plate, to offer high strenght cavity ;
9. For the complex mould which is difficult to demould, we can manufacture the automaitc mould with take out device ;
10. We produce the pattern sample to customer after finish the mould, when the pattern was qualified, then we do exceptance job for the mould ;
11. We have the Hexagon coordinate measuring instrument imported from the Switzerland to have a test make sure our mould qualified.